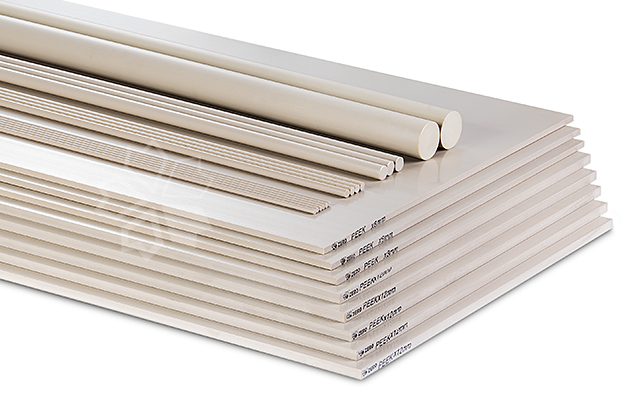
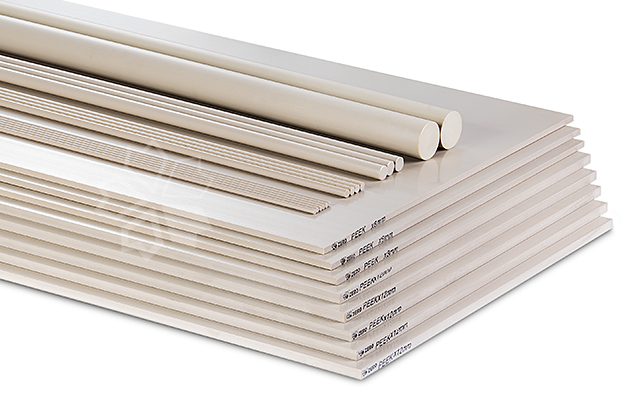
PEEK - VIRGIN RESIN
Polyether ether ketone (PEEK) is a representative variety of the poly aryl ether ketone (PAEK) family, a special engineering
plastic with excellent comprehensive properties. The rigid benzene ring and flexible ether bond in the molecular structure
of PEEK respectively provide excellent mechanical properties and abundant methods in molding as well as machining.
Zero Engineering has mass-produced PEEK sheets and rods since 2016. With independent technology, we designed everything from the production line of extrusion to tooling. We abandoned the traditional art of using fluorocarbon coating. New paint-coating shows higher adaptability on materials, helping the surface smooth and spot-free in the final product, which reduces the cost of milling the struggle spots during machining. Currently, the product has upgraded to the third generation. The trademark of this series is ZECAN®.
Zero Engineering has mass-produced PEEK sheets and rods since 2016. With independent technology, we designed everything from the production line of extrusion to tooling. We abandoned the traditional art of using fluorocarbon coating. New paint-coating shows higher adaptability on materials, helping the surface smooth and spot-free in the final product, which reduces the cost of milling the struggle spots during machining. Currently, the product has upgraded to the third generation. The trademark of this series is ZECAN®.
DETAILS
PERFORMANCE
- Maximum continuous operation temperature reaches 250℃ (the actual mechanical properties, strength, and modules would be obviously dropped after the glass transition temperature)
- Excellent mechanical properties, such as impact resistance, creep resistance, and abrasion resistance
- Except for concentrated sulfuric acid, it almost can withstand any other chemicals
- Radiation resistance is the best among all plastics (such as gamma rays)
- The material has self-extinguishment (UL94V-0) and strong UV resistance
- The highest steam resistance among all engineering plastics
- Comply with FDA certification, non-toxic
APPLICATIONS
- Electronic and electrical industries, IC wafer carriers, cleaning fixtures for a semiconductor device;
- Testing fixtures, LCD panel or equipment parts;
- Gears, bearings, piston rings, etc. for precision machinery and OA equipment;
- High-insulated terminal parts.
ATTENTIONS
- It is highly recommended to use both fiberglass and carbon fiber to ensure the airtightness of the material as well as the gap during machining.
- Weak resistance of concentrated sulfuric acid and hydrofluoric acid
SPECIFICATIONS (mm, g/cm³)
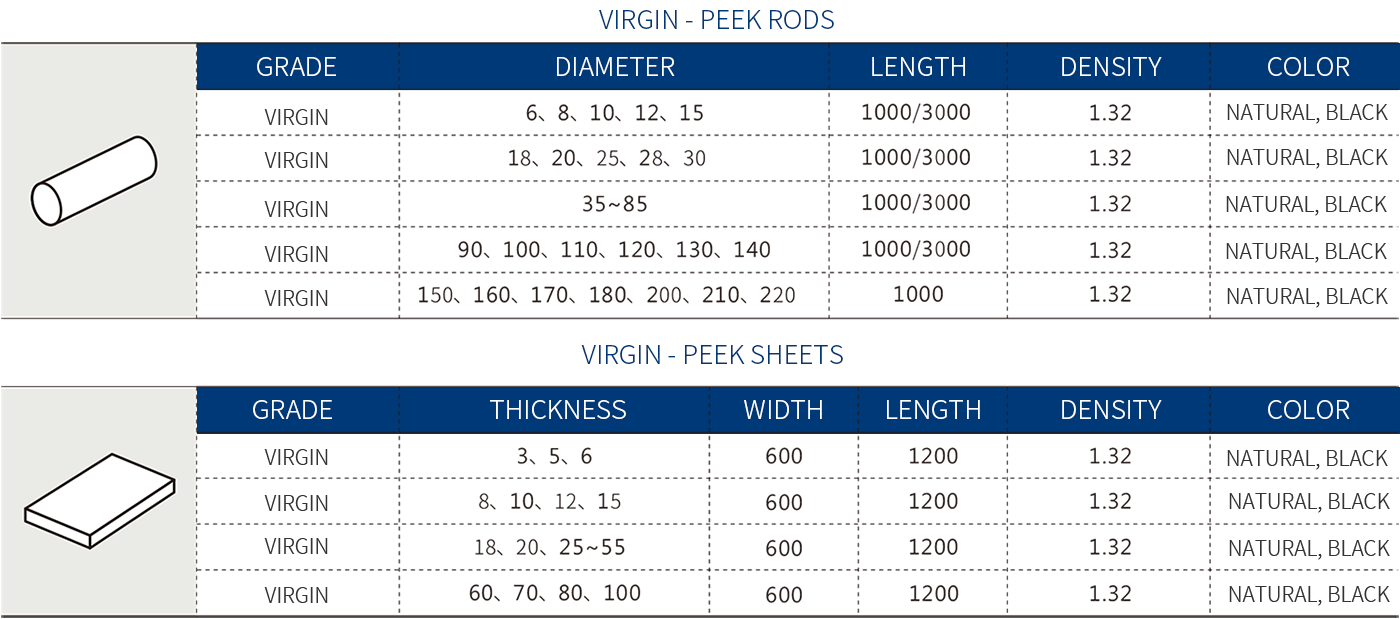